Fully automatic production line for tank trucks
In March 2015, Chengli Company spent 100 million yuan to build the world’s most advanced fully automated tank truck assembly line. This equipment is the first of its kind in China’s tank truck manufacturers. This assembly line greatly improves the production efficiency of tank trucks. At the same time, all the standard parts are used, which is easy to install and convenient for after sales.
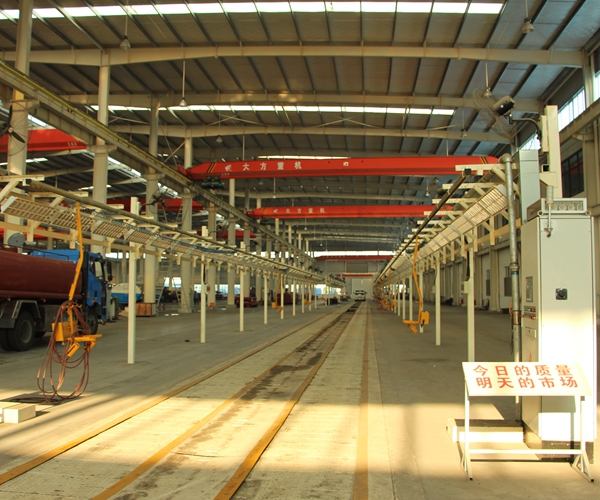
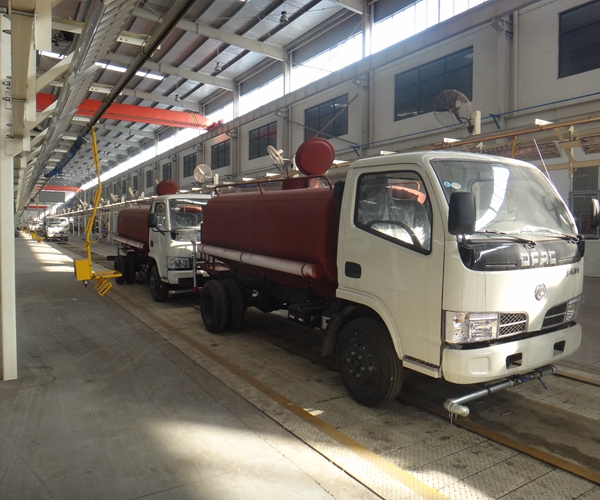
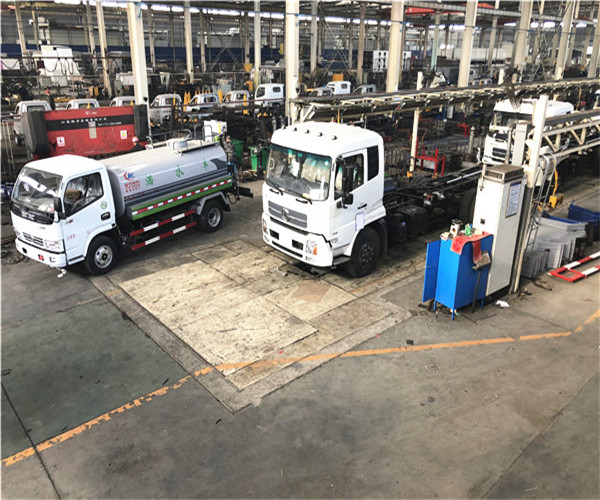
Truck baking paint workshop
In May 2015, Chengli Company spent 60 million yuan to introduce the truck paint workshop. The trucks produced by our company were pulled into the paint booth by automatic robots, and integrated with automatic painting and automatic drying. In the past, the mode of manual spraying was low in efficiency and unstable in quality. After two years, the paint fell off, but the automatic paint can be used for 5-8 years without falling off. In addition, in the past, manual paint spraying was carried out in industrial sheds, which caused great pollution to the surrounding environment. Chengli’s product also meets the requirements of energy conservation and emission reduction advocated by the world, and actively responds to the world’s environmental protection policies.
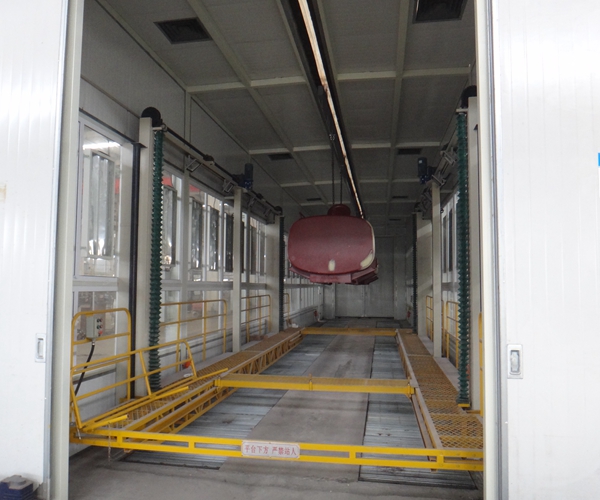
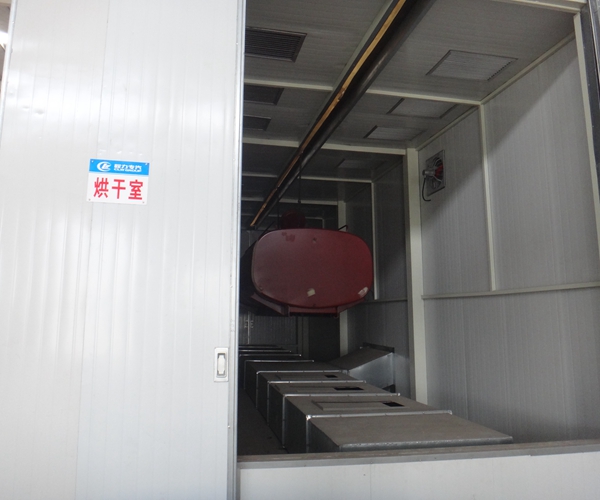
Seamless welding technology for tank trucks
Chengli Company seamless welding technology for tank trucks. The welding device converts the current 50 / 60Hz electrical frequency into 20KHz or 40KHz electrical energy high-frequency electrical energy through a transistor function equipment, and supplies it to the converter. The converter converts electrical energy into mechanical vibration energy for ultrasonic waves, and the voltage regulator is responsible for transmitting the converted mechanical energy to the welding head of the ultrasonic welding machine.
The welding head is an acoustic device that directly transmits the mechanical vibration energy to the product to be pressed. The vibration is transmitted to the bonding surface through the welding work piece. The friction and friction generate heat energy to melt the plastic. The vibration will stop when the molten material reaches its interface. Keeping the pressure for a short time can make the melt produce a strong molecular bond when the bonding surface is solidified. The entire cycle is usually completed in less than a second, but its welding strength is close to a continuous material.
Seamless welding technology can not only help eliminate the mold welding seam, but also improve the accuracy, smoothness and appearance of the parts accordingly. At the same time, the seamless welding technology implements efficient control during the injection molding process and shortens the mold processing cycle. Because the products produced by this process have excellent surface finish, there is no need to use secondary spraying and annealing, which avoids dimensional changes caused by secondary shrinkage.